Wednesday, August 6
Vacuum Success Leads to Energy Savings at Midland Plastics!
Midland Plastics is a manufacturer of performance plastics that has been around for over 75 years. They supply high quality plastic solutions that are lighter, more resistant, and longer lasting than traditional plastics for a variety of industries. This customer relies heavily on vacuum for their operations. They specifically utilize vacuum technology for thermoforming, part hold down, and drawing raw material down over tools, holding products for CNC trimming, and for their vacuum tables used in machining to hold product down without clamps.
-
Successful Technology
QSV 1100Es & an ECOntrol 3.0
-
Annual Cost Savings
Almost $9,000!
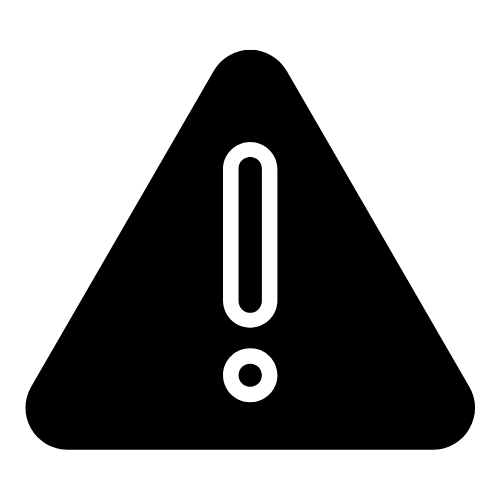
Overview of Problem
Midland Plastic’s old units were causing concerns for efficiency as they had observed growth since adding those units. This customer was unsure of the amount of vacuum their plant was using, and they believed that all 3 of their vacuum pumps had to be always running to accommodate their operations. They wanted to increase their efficiency and become more eco-friendly, so they called Zorn in to discuss their options- since Zorn has been servicing their 3 older 40hp vacuum pump units. Their designated Zorn sales representative, Bryan, discussed the topics of efficiency, stability, and reliability with them in regard to their vacuum usage, and recommended a full vacuum audit to fully understand their usage and needs.
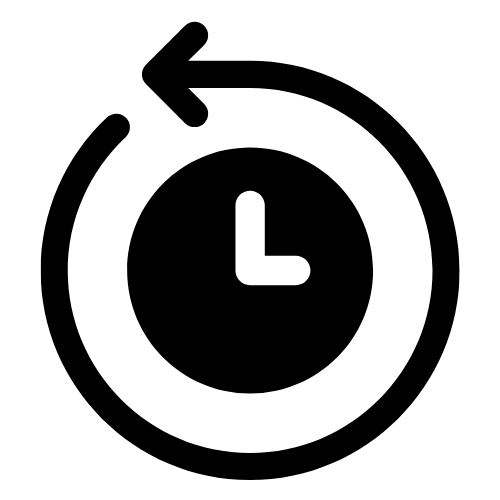
Previous Machines
Quincy QSVI-40 and (2) 40hp competitor fixed speed machines
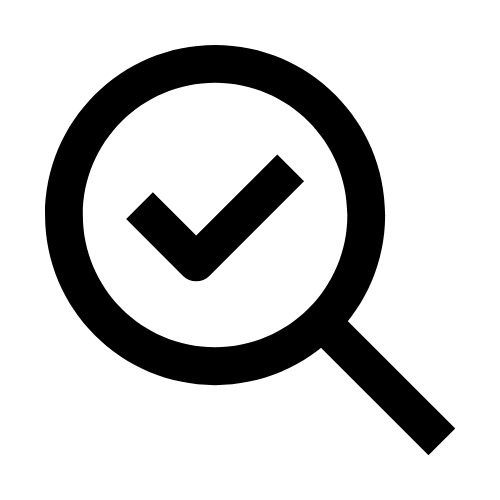
Zorn Vacuum Audit
Experienced Zorn technicians performed a full vacuum audit and compiled an in-depth report with their findings. This audit measured Midland’s vacuum level and motor amperage over the course of time. It was discovered that this customer requires an average of 553 ACFM at 24” HgV and peak flows up to 1,620 ACFM to meet their plant’s demand. This cost them roughly $22,191 per year.
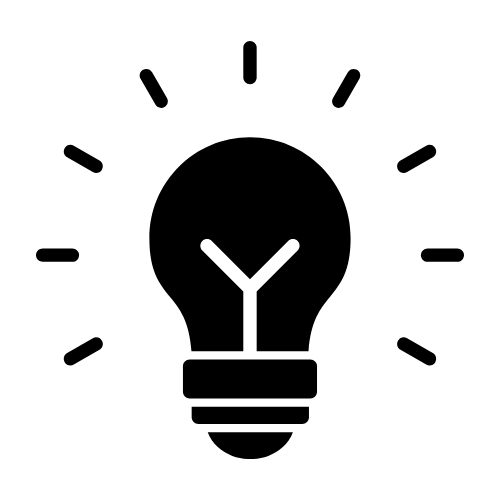
Zorn’s Solution
Zorn found that a Quincy QSV 1100E would properly meet the demand and consume about 17.5 hp less than the existing machines. This solution also presented major energy and cost savings of almost $9,000 annually in operating costs. Before this audit was conducted, this customer operated with two pumps to provide redundancy and be able to properly meet peak demand periods. These machines included (3) 40 hp fixed speed machines, each rated for 550 ACFM at 40hp compared to the QSV for 930ACFM at 50hp. Now, they can save energy, floor space, and improve their work environment by installing (2) QSV 1100E pumps and an ECOntrol 3.0 that allows (1) QSV 1100E to handle 95% of the customer’s demand and equally share the load 5% of the time when their peak usage requires two vacuum pumps. These QSV 1100E pumps are variable drive machines that are designed to meet your facility’s demand exactly at the minimum possible lifecycle cost.

End Result
Both Zorn Compressor & Equipment and the equipment manufacturer, Quincy Compressor, were able to work together to provide this customer with an efficient, logical, and clean installation to effectively meet and surpass their desired outcomes. This solution decreased the customer’s operating costs from $22,191 annually to $13,477 annually, provided quieter operations, and enhanced the cleanliness of the facility’s work environment for employees. Performing full-system audits provides precise data to guide informed decision making to optimize efficiencies, save money, and encourage growth.
The customer informed us that, "Maintaining a steadier vacuum pressure during our production processes significantly reduced material waste by ensuring more consistent and controlled operation. In the past, fluctuations in vacuum pressure would lead to defects such as incomplete seals—especially in our forming, machining, and CNC applications. This efficiency has not only conserved raw materials but also minimized downtime and boosted overall production quality."
Customer Review
“The whole process was very professional. There was always somebody to provide the answers at the appropriate level, from basic information to extreme technical information. The depth in Zorn Compressor and the people Zorn has in all areas seem to be top-notch.”
- Chuck H., General Manager