Energy Savings Case Study
This Trevor, Wisconsin customer was noticing constant maintenance issues, losses of efficiencies, and high energy costs with their old compressed-air systems. As they continued to increase production, they were in need of a more energy efficient, and durable solution.
-
ESTIMATED ANNUAL ENERGY COSTS
$18,512.62
-
ANNUAL ENERGY SAVINGS
17%
-
RETURN ON INVESTMENT IN
5.9 YEARS
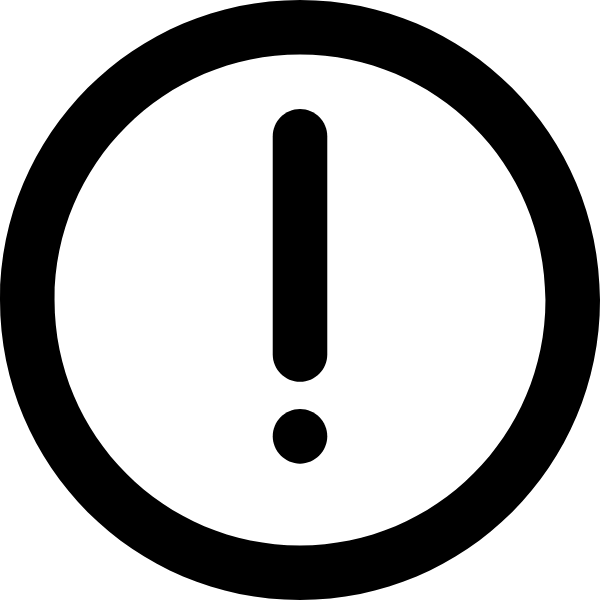
Challenge
This Wisconsin manufacturer that has been around for 60 years was operating with 2 older machines at lower capacities to keep up with their demand. They had a 25hp rotary screw compressor from 1996 and a 30hp piston compressor from 1993, both being very loud when operating. They used these machines for applications such as molding, receiving materials, and punch pressing. Maintenance costs were adding up, on top of energy costs causing them to re-evaluate their compressor situation.
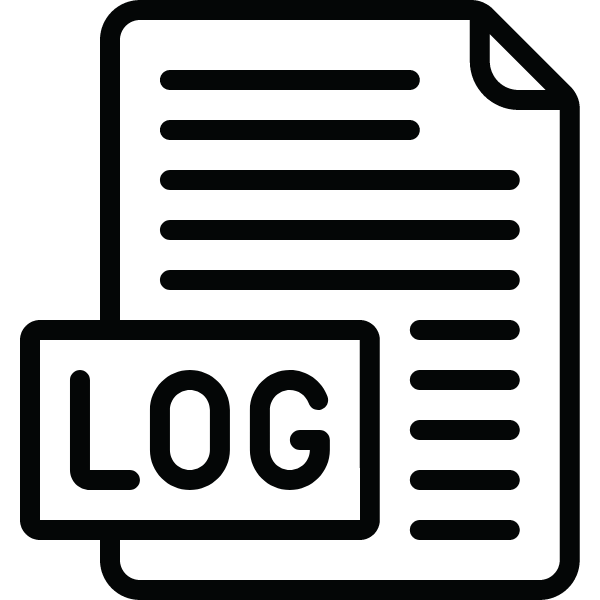
Process
This customer's Zorn Account Representative, Bryan, came in and performed a data logging to gain insight into true demand and energy consumption. Our Comprehensive Data Logging offering is a Full System Audit that evaluates the compressed air system's performance and overall efficiency to identify opportunities for improvement.
Bryan performed a week-long data logging, covering both first and second shifts. He started by installing the data logging equipment on each compressor in the system. After the week of collecting data on supply side and demand side necessities, they were provided with a personalized report covering the following:
- Operational cost based on the customers current electrical costs or reported blended electrical rate.
- Average power consumption and flow for the full logging period.
- Executive summary, to include current operating costs and cost reductions, based on implementation of any proposed recommendations and ROI.
- Daily graphs of data used throughout the duration of the survey.
- Demand-side evaluation of inappropriate compressed air uses.
- Analysis of identified system events
- Pressure Map for measured locations to identify piping/storage issues.
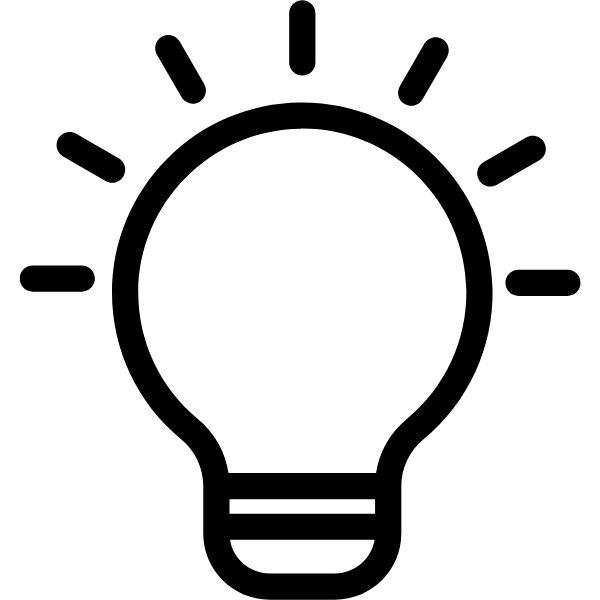
Solution
With Bryan's help and expertise, this customer upgraded to a new Quincy 60hp Variable Speed Rotary Screw Compressor (QGV 60) with a dryer. Because of their switch to a more energy efficient machine, this customer was able to obtain incentives from Focus on Energy to help pay for their upgrade. On top of the initial savings from the energy incentive, they now observe annual savings of about $4,000 in operational costs from utilizing one new, energy efficient machine. They keep their two older compressors as emergency backup. This new main machine also provides them with a quieter, more reliable operation overall.
Customer Review
"Zorn's service was great. The first time I met with Bryan, we hit it off and he helped me with finding the proper machines at the right cost....Not only do they put out a great product, but they are fair on pricing too."